Water treatment and disinfection in pharmaceutical water treatment
Ozone disinfection and sanitization of storage and distribution systems for pharmaceutical water
In the pharmaceutical industry, demineralized water is used for a wide variety of purposes in production and plant cleaning. The production and provision of constant and reliable water quality is of great economic and technical importance. According to the European Pharmacopoeia (PH. EUR), drinking water is prescribed as the starting medium. The different water qualities produced from this (PW Purified Water, HPW Highly Purified Water and WFI Water For Injection) are subject to strict quality criteria laid down in the pharmacopoeias.
Water treatment and ultrapure water production usually consists of the following main components that are pharmaceutically compliant:
- Backwashable prefiltration
- Double softening plant
- Two-stage reverse osmosis plant
- CO2 membrane degassing
- EDI electrodeionization
- Ultrafiltration at cold WFI generation designed by the plant engineering companies according to the water demand and special requirements of the pharmaceutical plant.
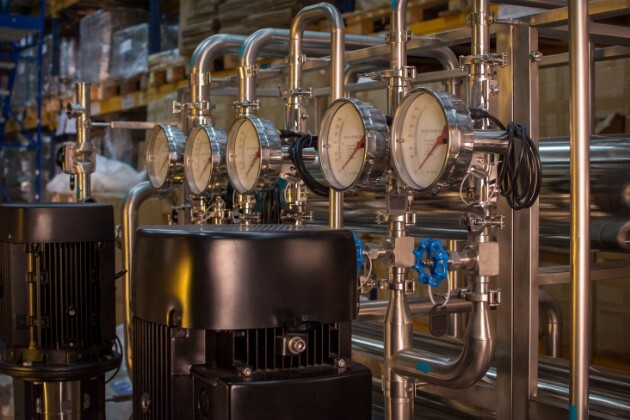
Illustration of an exemplary water treatment for pharmaceutical water
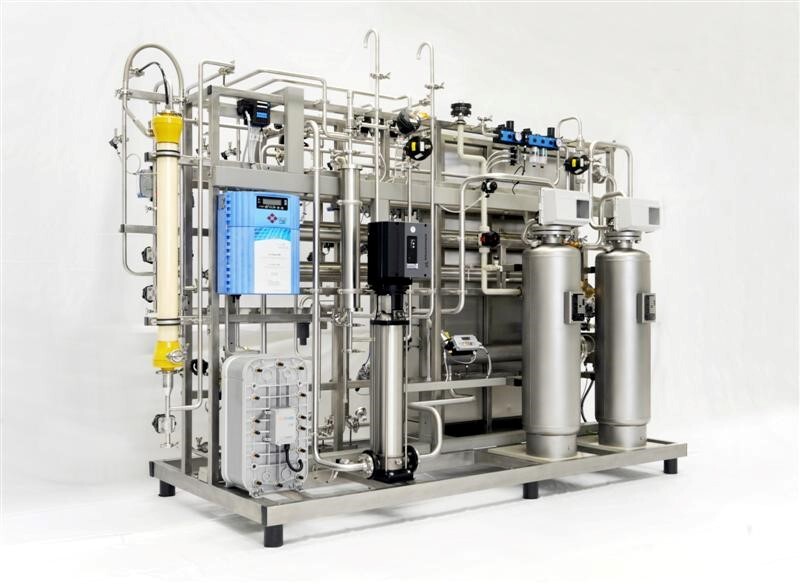
HPW generation plant; pre-assembled on frame and piped in stainless steel: 10 m3/h capacity: conductivity << 1 µS/cm and TOC values << 20 ppb.
Frequently, the treatment and generation plants are in continuous operation, thus producing water in stock. The water stored in tanks is pumped to the various consumption points via a ring main and returned to the tank via the return line.
The required water quality is not always a constant parameter in operational practice. The chemical and especially the microbiological water parameters – conductivity, TOC, bacterial counts (CFU/ml), endotoxins – can change due to various influencing factors in the storage and distribution system. Therefore, it is imperative that sustainable sanitization of the storage and distribution system is already taken into account during plant design.
It is considered an important goal to avoid, above all, an entry of microorganisms and associated contamination and potential biofilm formation.
Critical sources of contamination of ultrapure water are:
- Entry from the water treatment plant
- Ingress through system openings, such as fittings
- Back contamination via tapping points and valves
- Entry during installation and service work
To avoid these risky disruptive influences on pharmaceutical water quality in the ring main and in the tank, consistent measures must be planned, implemented and validated:
Materials and materials:
- Selection of suitable and permissible stainless steel components (1.4404, 1.4435) for pipeline and container construction; use of media-contacting fittings and instruments made of stainless steel or plastic materials (PTFE, PFA, PVDF) in accordance with pharma-compliant GMP criteria; redundant design if necessary.
- Pipeline and container construction taking into account low surface roughness (min. < 0.8 µm), freedom from dead space and avoidance of stubs.
Water disinfection and sanitization
- Determination of the disinfection procedure for the prevention of microbiological growth due to increase in bacterial counts and increase in bacterial endotoxins.
- Strategy for implementation of process engineering for water disinfection and sanitization of storage tank and ring main, especially for prevention of biofilm formation.
The use of suitable materials and equipment technology, such as instruments and fittings, for the construction and operation of a pharmaceutical water storage and distribution system is “state of the art” today. The quality of the metallic and polymer materials can be verified by material certificates according to DIN EN 10204 3.1 or 21 CfR 177ff (FDA conformity) and the EU Directive 1935/2004.
A hygienic design of the wetted parts is an integral part of the planning and implementation of a ring piping system.
Accordingly, unsuitable materials or materials of inferior quality should not be found in new designs and plant expansions. In older plants, e.g. with stub lines, this cannot be ruled out. For example, deposits or biofilms can form in poorly flowed pipe sections, which are not identified over a long period of time and result in quite a high risk if they break off due to flow or if microorganisms diffuse into the aqueous phase.
This problem clearly shows that the water matrix and especially the microbiological quality of the pharmaceutical water can change, partly in the short term due to a defective valve or insidiously due to unrecognized biofilm growth. Meanwhile, it has been proven that even at very low TOC levels, bacterial reproduction and the formation of biofilm matrices is possible, especially under sub-optimal hydraulic conditions and flow conditions.
The financial burdens and damage caused by water throwing, pipeline cleaning, replacement of components and the associated plant and production downtime can be enormous. Therefore, it is imperative to develop and technically implement a comprehensive concept for reliable disinfection of the stored pharmaceutical water with sanitization of the ring main.
Continuous UV irradiation of the circulating water is not sufficient to ensure reliable network protection of the tank volume and ring line. The germicidal effect of UV radiation at 254 nm is limited to the irradiation field of the UV reactor.
In operational practice, several sanitization processes are used to maintain the microbiological quality of the water stored and to be distributed. For cold-stored PW and HPW systems, hot water sanitization at 85 °C and, increasingly, ozonation are used; for WFI, pure steam sanitization, pressurized hot water sanitization at 121 °C, and, for newer cold-operated systems, ozonation.
Pure steam and pressurized hot water:
Pure steam is produced by various evaporation processes and, like the generation of hot water under pressure, has proven itself for many decades as a recognized method for sanitization and/or hot storage. The plant and insulation technology can definitely be considered complex and the investment and operating costs higher than for hot water or ozone sanitization.
Hot water
The production of hot water by means of heat exchangers is a common method for periodic thermal sanitization of PW and HPW loop systems. The installation cost is usually low and the effective energy cost depends on the frequency of heating.
Ozonation
Ozone as a biocide dissolved in water completely fulfills the requirements for sustained reliable water quality in the storage tank and in the pipeline. Ozone offers the advantage over thermal sanitization that 99% of the water in the system can be constantly exposed to low ozone concentrations in the storage tank. This makes storage with ozone equivalent to a self-sanitizing system, comparable to a WFI with hot storage.
Electrolytically generated ozone
Ozone is produced electrolytically on site in situ from ultrapure water and mixed directly into the ring main. Ozone is considered the strongest technically applicable disinfectant with a very high oxidation potential (EOP 2.08). Effectiveness on microbiological growth has been demonstrated in the range of 20-50 ppb dissolved ozone.
Electrolytically generated ozone has been used very successfully for many years in PW or HPW storage and distribution systems operated without thermal sanitization. The process is characterized by high reliability, operational safety and low energy consumption.
The cold production of WFI by means of membrane plants is now permitted according to American USP and European Pharmacopoeias. The plant technology uses ultrafiltration as the final microbiological barrier and allows reduced operating costs and significantly lower energy consumption compared to distillation technology. Accordingly, WFI can be reliably stored cold (15-25 °C) under low ozone concentrations in the tank and pumped to the points of consumption in the ring main.
Electrolytic ozone generation takes place in a compact flow-through electrolytic cell with built-in special electrodes (anode, cathode, solid electrolyte). Based on the principle of catalytic water electrolysis, oxygen/ozone is produced anodically and hydrogen is produced cathodically. The semi-permeable membrane acts as electrolyte and separator at the same time and is installed between the porous anode and cathode disks:
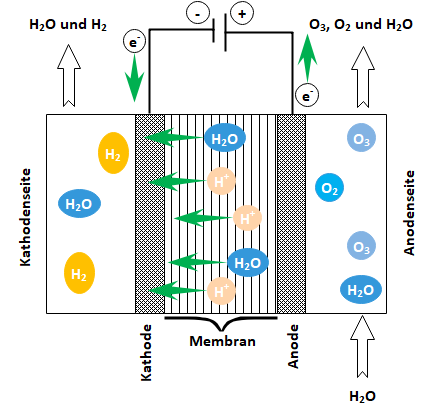
Schematic structure of the electrolytic cell with anode and cathode processes
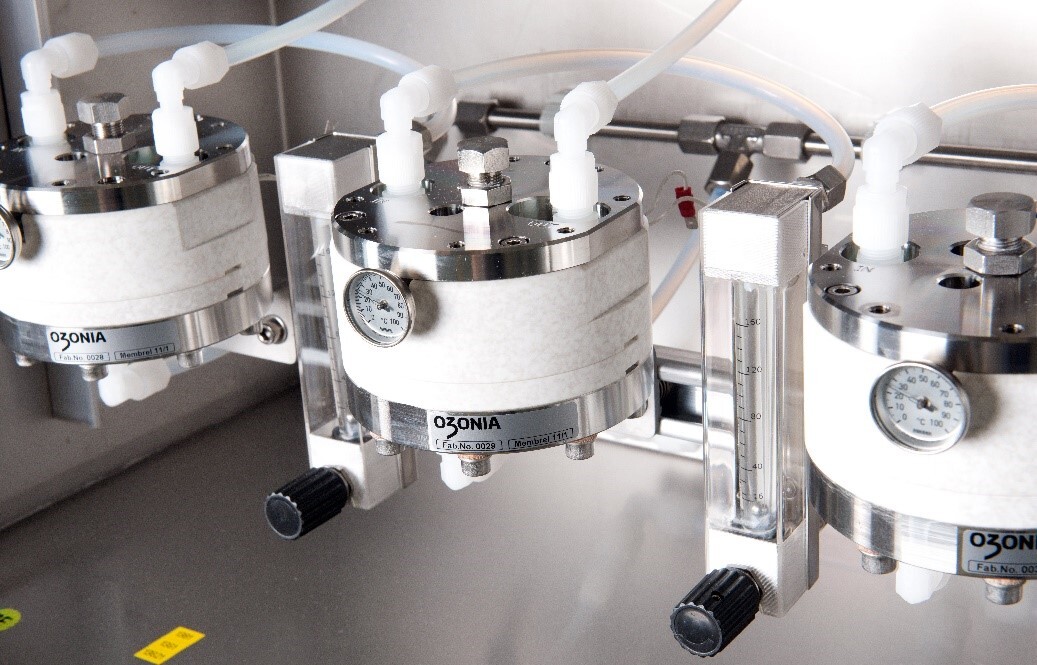
MkIV electrolysis cells with flow meter; max. 4 g/h ozone
An ozone cell with an active anode surface of approx. 30 cm2 generates max. 4 g/h ozone at 60 A electrolysis current and 100 l/h ultrapure water flow rate. The ozone produced in gaseous form at the anode dissolves into the continuous water flow and is fed from the bypass line of the electrolysis cell to the storage and distribution system. The technical effort for ozone generation and mixing into the ultrapure water is low. No operating gas, air or oxygen, as in conventional ozone generators, and no injector or diffuser technology is required to dissolve ozone in the water. The ozone-containing water is mixed with the main stream and disperses into the storage tank via a submersible lance.
A UV system with low-pressure lamps is installed in the feed line of the ring line to reliably convert the physically dissolved ozone into oxygen by photochemical splitting at a wavelength of 254 nm. At the sampling points, the pharmaceutical water must be verifiably ozone-free. Continuous monitoring of the ozone-free water and the ozone concentrations in the flow and return of the ring line is carried out continuously with amperometric measuring probes or UV photometers.
Figure 4 shows schematically the main water treatment components for the production of PW or HPW and the structure of a storage and distribution system with electrolytic ozone generator, UV system for the decomposition of dissolved ozone and ozone measurement technology QIC.
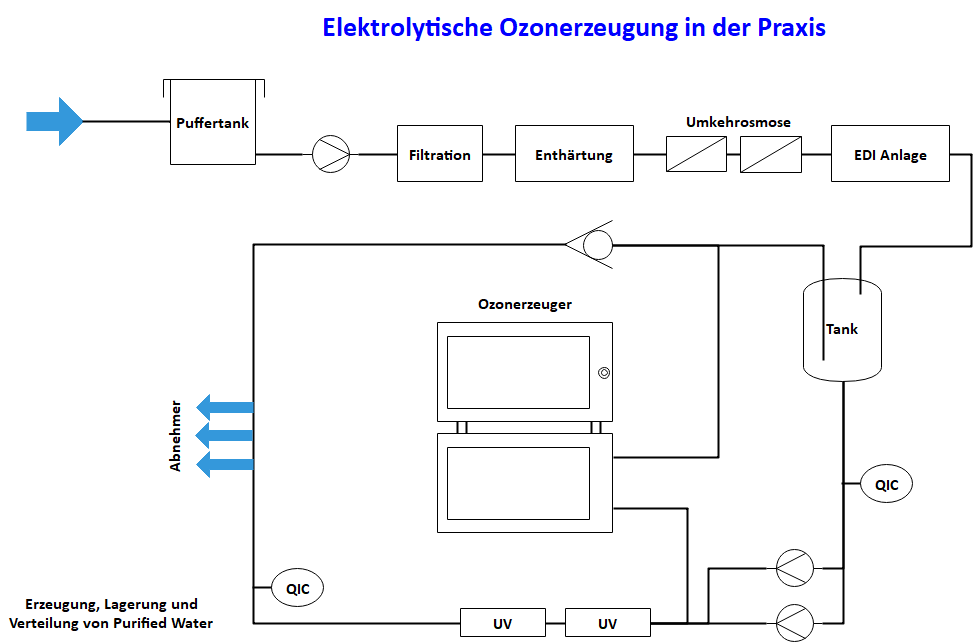
Construction of a pharmaceutical water production plant with tank and ring line; incl. ozone generator, UV systems and ozone measuring technology
The exhaust air from the tank may contain gaseous ozone, which should be catalytically destroyed downstream of the sterile filter installed in the exhaust line. The ozone destroyer reactors are installed in the line and work with a specific ozone catalyst made of mixed oxide or precious metal granules.
As a rule, the storage tank is continuously exposed to 30 – 50 ppb ozone in many systems, thus protecting the largest volume of water in the system from microbiological contamination.
Periodic ozone sanitization of the ring line is always possible when no removal of the ultrapure water is required, e.g. at night or on weekends. The UV system is switched off and the entire ring line and tank are exposed to ozone over an adjustable period of time. A successful sanitization process can be assumed if a setpoint value of, for example, 80 ppb ozone is continuously measured in the return flow over a time interval of, for example, 5 hours. The operator can check and evaluate the ozone dose required for the specific plant (concentration x time period) on the basis of simultaneously measured data on microbiological contamination and TOC concentrations.
The electrical power consumption for the production of 4 g/h of ozone is very low compared to the generation of heat at 121 °C or sterile steam and amounts to approx. 300 W, i.e. approx. 75 W/g ozone. A loop system with a 20 m3 storage tank can be reliably protected from microbiological contamination and biofilm formation with an adjustable ozone output of max. 4 g/h power.
The ozone system technology is designed according to the specification and hydraulic data of the storage and distribution system and consists of the following main components integrated in the ring piping system:
Electrolytic ozone generator MkIV
Generator system with integrated, adjustable electrolysis cells (1, 2 or 3 pcs.), max. 4 g/h ozone per cell
UV systems UVprofessional PHARMA
Stainless steel reactors with single and multi-jet low-pressure emitters for the decomposition of dissolved ozone, incl. calibrated UV sensor system
Catalytic residual ozone destruct OzonDestruct
Reactor system with mixed oxide catalyst filling and supply air heating for the vessel exhaust air
Online measurement technology for dissolved ozone and ambient air monitoring
Amperometric and electrochemical sensor technology for measurements in the liquid and gas phase
Contact
Please contact us if you are interested in detailed technical documentation on the equipment technology we can supply to suit your application for pharmaceutical water disinfection and sanitization.
Do you need advice?
- You are planning a new storage and distribution system for PW, HPW or WFI cold or would like to expand your existing system and would like advice on ozone as an effective disinfection and sanitization method
- You are interested in ozonation and need support in engineering, plant design and process planning
- Do you have specific questions about the investment and operating costs of ozone plant technology, its cost-effectiveness, safety and comparison with other disinfection and sanitization processes?
- Which operating modes are possible and how should the plant control be designed? Do you need support in questions of automation and integration of suitable measurement and control technology?
- You operate an existing ozone plant and would like support in assessing ozone effectiveness and water quality, plant operation and operational safety
- Maintenance and system servicing: We will be happy to carry out an inventory at an on-site appointment and plan system optimization and measures for sustainable service together with you.
Your direct contact:
Manager Solution Building
Mr. Karsten Hesse
Phone: + 49 (0) 5121 7609-75
E-Mail: hesse@heylneomeris.de