Wasseraufbereitung und Desinfektion in der Pharmawasseraufbereitung
Ozondesinfektion und -sanitisierung von Lager- und Verteilsystemen für Pharmawasser
In der pharmazeutischen Industrie wird vollentsalztes Wasser für verschiedenste Zwecke in der Produktion und Anlagenreinigung verwendet. Die Herstellung und Bereitstellung einer konstanten und zuverlässigen Wasserqualität ist von großer wirtschaftlicher und technischer Bedeutung. Als Ausgangsmedium ist gemäß Europäischem Arzneibuch (PH. EUR) Trinkwasser vorgeschrieben. Die daraus erzeugten unterschiedlichen Wasserqualitäten (PW Purified Water, HPW Highly Purified Water und WFI Water For Injection) unterliegen strengen, in den Arzneibüchern estgelegten Qualitätskriterien.
Die Wasseraufbereitung und Reinstwassererzeugung besteht in der Regel aus den folgenden pharmakonformen Hauptkomponenten:
- Rückspülbare Vorfiltration
- Doppel-Enthärtungsanlage
- Zweistufige Umkehrosmoseanlage
- CO2-Membran-Entgasung
- EDI Elektrodeionisation
- Ultrafiltration bei kalter WFI Erzeugung, die von den Anlagenbauunternehmen entsprechend dem Wasserbedarf und den speziellen Anforderungen des Pharmabetriebs ausgelegt werden.
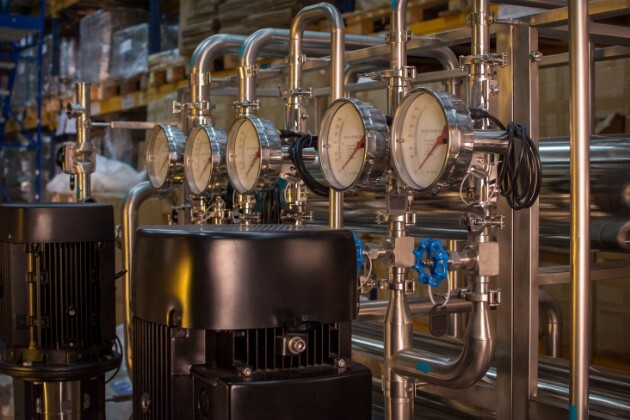
Abbildung einer beispielhaften Wasseraufbereitung für Pharmawasser
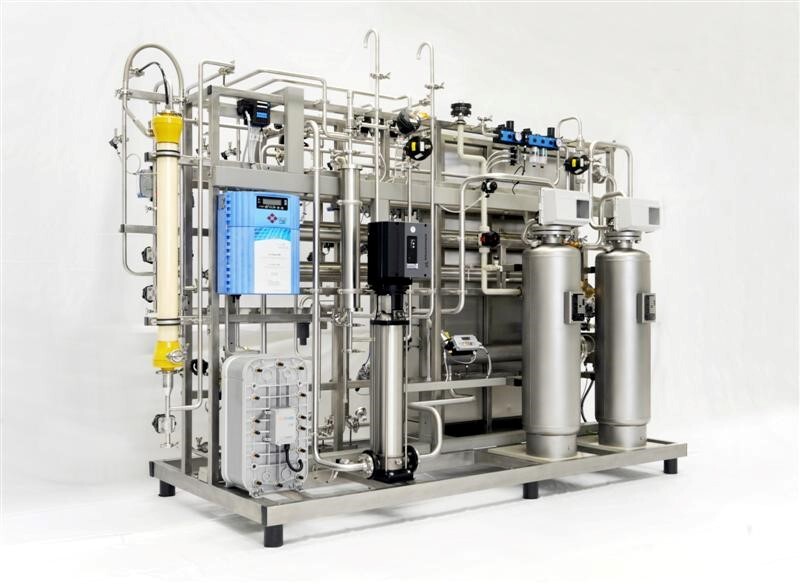
HPW Erzeugungsanlage; auf Rahmen vormontiert und in Edelstahl verrohrt: 10 m3/h Leistung: Leitfähigkeit << 1 µS/cm und TOC Werte << 20 ppb
Häufig sind die Aufbereitungs- und Erzeugungsanlagen kontinuierlich in Betrieb, produzieren somit Wasser auf Vorrat. Das in Tanks gelagerte Wasser wird über eine Ringleitung zu den diversen Verbrauchsstellen gepumpt und über den Rücklauf zum Tank zurückgeführt.
Die erforderliche Wasserqualität ist in der betrieblichen Praxis nicht immer eine gleichbleibende konstante Größe. Die chemischen und vor allem die mikrobiologischen Wasserparameter – Leitfähigkeit, TOC, Keimzahlen (KBE/ml), Endotoxine – können sich aufgrund verschiedener Einflussfaktoren im Lager- und Verteilsystem verändern. Deshalb ist es zwingend erforderlich, dass bereits bei der Anlagenplanung eine nachhaltige Sanitisierung des Lager- und Verteilsystems berücksichtigt wird.
Es gilt als wichtiges Ziel, vor allem einen Eintrag von Mikroorganismen und eine damit verbundene Kontamination und potenzielle Biofilm-Bildung zu vermeiden.
Kritische Quellen für eine Verkeimung des Reinstwassers sind:
- Eintrag aus der Wasseraufbereitungsanlage
- Eindringen durch Systemöffnungen, wie Armaturen
- Rückverkeimung über Entnahmestellen und Ventile
- Eintrag bei Installations- und Servicearbeiten
Um diese riskanten Störeinflüsse auf die Pharmawasser-Qualität in der Ringleitung und im Tank zu vermeiden, müssen konsequente Maßnahmen eingeplant, umgesetzt und validiert werden:
Materialien und Werkstoffe:
- Auswahl der geeigneten und zulässigen Edelstahlkomponenten (1.4404, 1.4435) für Rohrleitungs- und Behälterbau; Verwendung von medienberührenden Armaturen und Instrumente aus Edelstahl oder Kunststoffmaterialien (PTFE, PFA, PVDF) nach pharmakonformen GMP Kriterien; ggfs. in redundanter Ausführung.
- Rohrleitungs- und Behälterbau unter Berücksichtigung einer geringen Oberflächenrauigkeit (mind. < 0,8 µm), Totraum-Freiheit und Vermeidung von Stichleitungen
Wasserdesinfektion und Sanitisierung
- Festlegung des Desinfektionsverfahren für die Vermeidung von mikrobiologischen Wachstum durch Anstieg der Keimzahlen und Zunahme von Bakterien-Endotoxinen.
- Strategie zur Implementierung der Verfahrenstechnik für die Wasserdesinfektion und Sanitisierung von Lagertank und Ringleitung, insbesonders zur Vermeidung der Biofilm-Bildung.
Die Verwendung geeigneter Materialien und Gerätetechnik, wie Instrumente und Armaturen, für den Aufbau und Betrieb eines Pharmawasser – Lager- und Verteilsystems ist heute “Stand der Technik”. Die Qualität der metallischen und polymeren Werkstoffe lässt sich durch Material-Zeugnisse nach DIN EN 10204 3.1 bzw. 21 CfR 177ff (FDA Konformität) und der EU-Richtlinie 1935/2004 nachweisen.
Ein hygienisches Design der medienberührten Teile ist integrativer Bestandteil der Planung und Umsetzung eines Ringleitungssystems.
Dementsprechend sollten sich bei Neuplanungen und Anlagenerweiterungen keine ungeeignete Materialien oder Werkstoffe minderer Qualität finden. In älteren Anlagen, z.B. mit Stichleitungen, ist dies nicht auszuschließen. So können sich z.B. in schlecht durchströmten Leitungsabschnitten Ablagerungen bzw. Biofilme bilden, die über eine lange Zeit nicht identifiziert werden und ein durchaus hohes Risiko ergeben, wenn sie strömungsbedingt abreißen oder wenn Mikroorganismen in die wässrige Phase diffundieren.
Diese Problematik zeigt eindeutig, dass sich die Wassermatrix und vor allem die mikrobiologische Qualität des Pharmawassers ändern kann, teils kurzfristig durch ein defektes Ventil oder schleichend durch ein nicht erkanntes Biofilmwachstum. Mittlerweile ist nachgewiesen, dass selbst bei sehr niedrigen TOC Werten eine Bakterien-Reproduktion und die Bildung von Biofilm-Matrices möglich ist, vor allem unter sub-optimalen hydraulischen Bedingungen und Strömungsverhältnissen.
Die finanziellen Belastungen und Schäden durch Wasserverwurf, Rohrleitungsreinigung, Austausch von Komponenten und der damit verbundene Anlagen- und Produktionsstillstand können enorm sein. Deswegen ist es zwingend erforderlich, ein umfassendes Konzept für die zuverlässige Desinfektion des gelagerten Pharmawassers mit einer Sanitisierung der Ringleitung zu entwickeln und technisch umzusetzen.
Eine kontinuierliche UV-Bestrahlung des zirkulierenden Wassers reicht nicht aus, um einen zuverlässigen Netzschutz von Tankvolumen und Ringleitung zu gewährleisten. Die keimabbauende Wirkung der UV-Strahlung bei 254 nm ist auf das Bestrahlungsfeld des UV-Reaktors begrenzt.
In der betrieblichen Praxis werden mehrere Sanitisierungsverfahren zur Aufrechterhaltung der mikrobiologischen Qualität des gelagerten und zu verteilenden Wassers eingesetzt. Bei kaltgelagerten PW und HPW Systemen wird die Heißwassersanitisierung bei 85 °C und immer häufiger die Ozonisierung verwendet; bei WFI die Reinstdampfsanitisierung, die Druckheißwassersanitisierung bei 121 °C und bei neueren kalt betriebenen Anlagen die Ozonisierung.
Reinstdampf und Druckheißwasser:
Reinstdampf wird nach verschiedenen Verdampferverfahren hergestellt und hat sich, wie die Erzeugung von Heißwasser unter Druck, seit vielen Jahrzehnten als anerkannte Methode zur Sanitisierung und/oder Heißlagerung bewährt. Die Anlagen- und Isolationstechnik ist durchaus als aufwendig zu bewerten und die Investitions- und Betriebskosten höher als bei der Heißwasser- oder Ozonsanitisierung.
Heißwasser
Die Erzeugung von Heißwasser mittels Wärmetauscher ist ein verbreitetes Verfahren für die periodische thermische Sanititisierung von PW und HPW Ringleitungssystemen. Der Installationsaufwand ist meist gering und die effektiven Energiekosten von der Häufigkeit der Aufheizung abhängig.
Ozonisierung
Ozon als in Wasser gelöstes Biozid erfüllt vollständig die Anforderungen an eine nachhaltig zuverlässige Wasserqualität im Lagerbehälter und in der Rohrleitung. Ozon bietet den Vorteil gegenüber der thermischen Sanitisierung, dass 99 % des im System befindlichen Wassers ständig mit niedrigen Ozonkonzentrationen im Lagertank beaufschlagt werden kann. Dadurch entspricht die Lagerung mit Ozon einem self-sanitizing system, vergleichbar einem WFI mit Heißlagerung.
Elektrolytisch erzeugtes Ozon
Ozon wird aus dem Reinstwasser elektrolytisch vor Ort in situ produziert und direkt in die Ringleitung eingemischt. Ozon gilt als stärkstes technisch einsetzbares Desinfektionsmittel mit sehr hohem Oxidationspotential (EOP 2,08). Die Wirksamkeit auf mikrobiologisches Wachstum ist im Bereich von 20-50 ppb gelöstes Ozon nachgewiesen.
Seit vielen Jahren wird in PW bzw. HPW Lager- und Verteilsystemen, die ohne thermische Sanitisierung betrieben werden, sehr erfolgreich elektrolytisch erzeugtes Ozon eingesetzt. Das Verfahren zeichnet sich durch hohe Zuverlässigkeit, Betriebssicherheit und niedrigen Energieeinsatz aus.
Die kalte Herstellung von WFI mittels Membrananlagen ist mittlerweile nach amerikanischer USP und Europäischen Arzneibüchern zulässig. Die Anlagentechnik arbeitet mit einer Ultrafiltration als letzte mikrobiologische Barriere und ermöglicht reduzierte Betriebskosten und deutlich geringeren Energieaufwand im Vergleich zur Destillationstechnik. Dementsprechend lässt sich WFI zuverlässig kalt (15-25 °C) unter niedrigen Ozonkonzentrationen im Tank lagern und zu den Verbrauchsstellen in der Ringleitung pumpen.
Die elektrolytische Ozonerzeugung erfolgt in einer kompakten Durchfluss-Elektrolysezelle mit eingebauten Spezial-Elektroden (Anode, Kathode, Feststoff-Elektrolyt). Nach dem Prinzip der katalytischen Wasserelektrolyse wird anodisch Sauerstoff/Ozon und kathodisch Wasserstoff erzeugt. Die semi-permeable Membran wirkt als Elektrolyt und Separator gleichzeitig und wird zwischen den porösen Anoden- und Kathodenscheiben eingebaut:
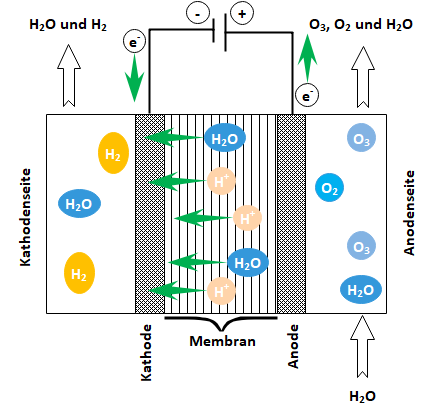
Schematischer Aufbau der Elektrolysezelle mit Anoden- und Kathodenprozessen
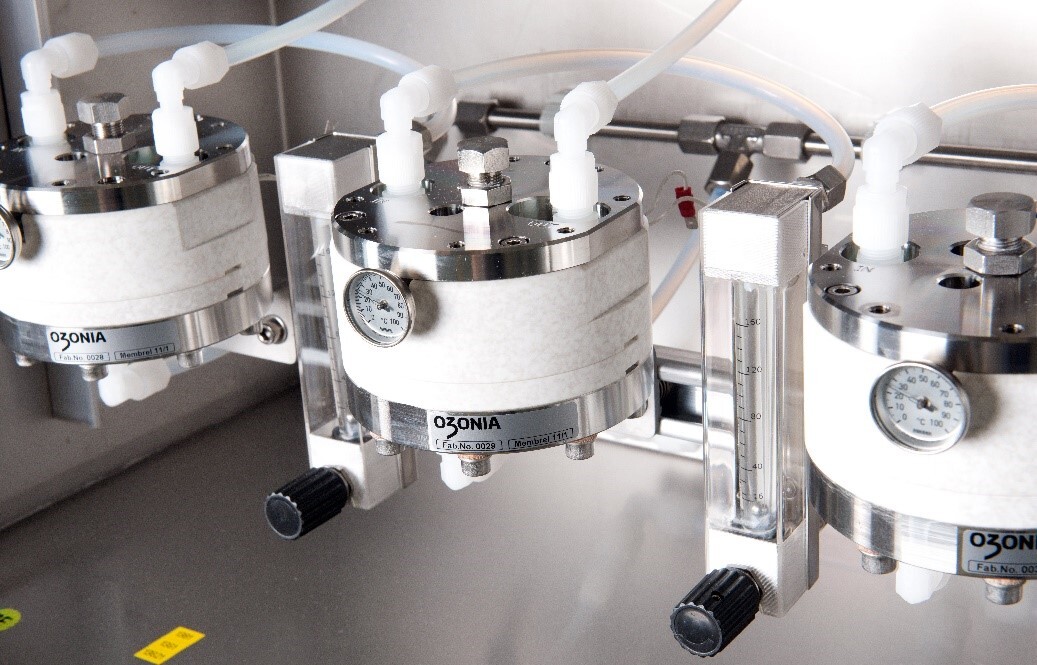
MkIV-Elektrolysezellen mit Durchflussmesser; max. 4 g/h Ozon
Eine Ozonzelle mit einer aktiven Anodenoberfläche von ca. 30 cm2 erzeugt bei 60 A Elektrolysestrom und 100 l/h Reinstwasser-Durchfluss max. 4 g/h Ozon. Das gasförmig an der Anode entstehende Ozon löst sich in den kontinuierlichen Wasserstrom und wird aus der Bypass-Leitung der Elektrolysezelle dem Lager- und Verteilsystem zugeführt. Der technische Aufwand für die Ozonerzeugung und das Einmischen in das Reinstwasser ist gering. Es wird kein Betriebsgas, Luft oder Sauerstoff, wie bei konventionellen Ozongeneratoren, und keine Injektor- oder Diffusortechnik zum Lösen von Ozon im Wasser benötigt. Das ozonhaltige Wasser wird mit dem Hauptstrom vermischt und verteilt sich über eine Tauchlanze im Lagerbehälter.
Im Vorlauf der Ringleitung wird eine UV-Anlage mit Niederdruckstrahlern eingebaut, um das physikalisch gelöste Ozon durch photochemische Spaltung bei 254 nm Wellenlänge zuverlässig in Sauerstoff umzuwandeln. An den Entnahmestellen muss das Pharmawasser nachweislich ozonfrei sein. Die kontinuierliche Überwachung des ozonfreien Wassers und der Ozonkonzentrationen im Vor- und Rücklauf der Ringleitung erfolgt kontinuierlich mit amperometrischen Messonden oder UV-Photometern.
Abbildung 4 zeigt schematisch die wichtigsten Wasseraufbereitungskomponenten für die Herstellung von PW oder HPW und den Aufbau eines Lager- und Verteilsystems mit Elektrolytischem Ozongenerator, UV-Anlage zum Abbau von gelöstem Ozon und Ozon-Messtechnik QIC.
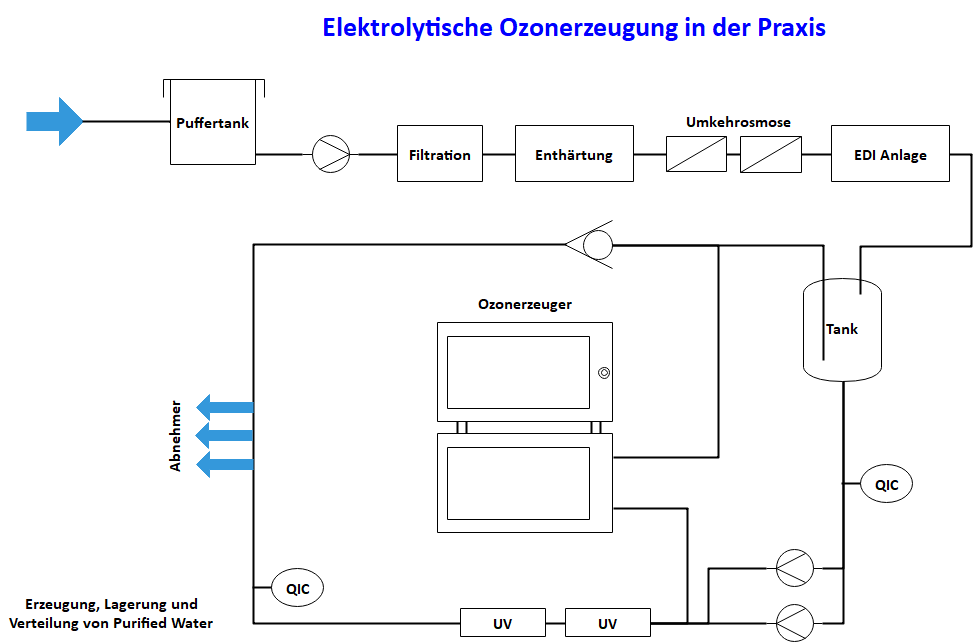
Aufbau einer Pharmawasser-Erzeugungsanlage mit Tank und Ringleitung; inkl. Ozonerzeuger, UV-Anlagen und Ozonmesstechnik
Die Abluft des Tanks kann gasförmiges Ozon enthalten, das katalytisch hinter dem in der Abluftleitung eingebauten Sterilfilter zerstört werden sollte. Die Ozonvernichter-Reaktoren werden in die Leitung eingebaut und arbeiten mit einem spezifischen Ozonkatalysator aus Mischoxid- oder Edelmetall-Granulat.
In der Regel wird der Lagertank kontinuierlich bei vielen Anlagen mit 30 – 50 ppb Ozon beaufschlagt und damit das größte Wasservolumen des Systems vor mikrobiologischer Verkeimung geschützt.
Eine periodische Ozon-Sanitisierung der Ringleitung ist immer dann möglich, wenn keine Abnahme des Reinstwasser erforderlich ist, also z.B. nachts oder am Wochenende. Die UV-Anlage wird ausgeschaltet und über einen einstellbaren Zeitraum die gesamte Ringleitung und der Tank mit Ozon beaufschlagt. Es kann von einem erfolgreichen Sanitisierungsprozess ausgegangen werden, wenn ein Sollwert von z.B. 80 ppb Ozon kontinuierlich über ein Zeitintervall von beispielsweise 5 Stunden im Rücklauf gemessen wird. Eine Überprüfung und Bewertung der anlagenspezifisch erforderlichen Ozondosis (Konzentration x Zeitraum) ist betreiberseitig aus zeitgleich erhobenen Messdaten der mikrobiologischen Keimbelastung und der TOC Konzentrationen möglich.
Die elektrische Leistungsaufnahme für die Produktion von 4 g/h Ozon ist im Vergleich zur Erzeugung von Hitze bei 121 °C oder Sterildampf sehr gering und beträgt ca. 300 W, also ca. 75 W/g Ozon. Ein Ringleitungssystem mit einem 20 m3 Lagertank kann zuverlässig mit einer regelbaren Ozonleistung von max. 4 g/h Leistung vor mikrobiologischer Kontamination und Biofilm-Bildung geschützt werden.
Die Ozonanlagentechnik wird auf die Spezifikation und hydraulischen Daten des Lager- und Verteilsystem ausgelegt und besteht aus Folgenden, im Ringleitungssystem integrierten Hauptkomponenten:
Elektrolytischer Ozongenerator MkIV
Generatorsystem mit integrierten, regelbaren Elektroysezellen (1, 2 oder 3 Stk.), max. 4 g/h Ozon pro Zelle
UV-Anlagen UVprofessional PHARMA
Edelstahlreaktoren mit Ein- und Mehrstrahler-Niederdruckstrahler für den Abbau von gelöstem Ozon, inkl. kalibrierte UV-Sensorsystem
Katalytische Restozonvernichter OzonDestruct
Reaktorsystem mit Mischoxid-Katalysatorfüllung und Zuluft Heizung für die Behälter-Abluft
Online-Messtechnik für gelöstes Ozon und Raumluftüberwachung
Amperometrische und elektrochemische Sensorik für Messungen in der Flüssig- und Gasphase
Kontaktieren Sie uns bei Interesse an detaillierten technischen Unterlagen über die von uns lieferbaren Gerätetechnik passend für Ihren Anwendungsfall zur Pharmawasser-Desinfektion und Sanitisierung.
Sie haben Beratungsbedarf?
- Sie planen ein neues Lager- und Verteilsystem für PW, HPW oder WFI kalt oder möchten Ihre bestehende Anlage erweitern und wünschen Beratung über Ozon als wirkungsvolles Desinfektions- und Sanitisierungsverfahren
- Sie interessieren sich für die Ozonisierung und benötigen Unterstützung beim Engineering, Anlagenauslegung und Verfahrensplanung
- Sie haben konkrete Fragen zu den Investitions- und Betriebskosten der Ozonanlagentechnik, zur Wirtschaftlichkeit, Sicherheit und zum Vergleich mit anderen Desinfektions- und Sanitisierungsverfahren?
- Welche Betriebsweisen sind möglich und wie soll die Anlagensteuerung konzipiert werden? Benötigen Sie Unterstützung bei Fragen der Automatisierung und Einbindung geeigneter Mess- und Regeltechnik?
- Sie betreiben eine bestehende Ozonanlage und wünschen Unterstützung zur Beurteilung der Ozonwirksamkeit und der Wasserqualität, von Anlagenbetrieb und Betriebssicherheit
- Instandhaltung und Anlagenwartung: Gerne führen wir bei einem Vor Ort Termin eine Bestandsaufnahme durch und planen gemeinsam mit Ihnen die Systemoptimierung und Maßnahmen für nachhaltigen Service
Ihr direkter Ansprechpartner:
Leiter Solution Building
Herr Karsten Hesse
Telefon: + 49 (0) 5121 7609-75
E-Mail: hesse@heylneomeris.de